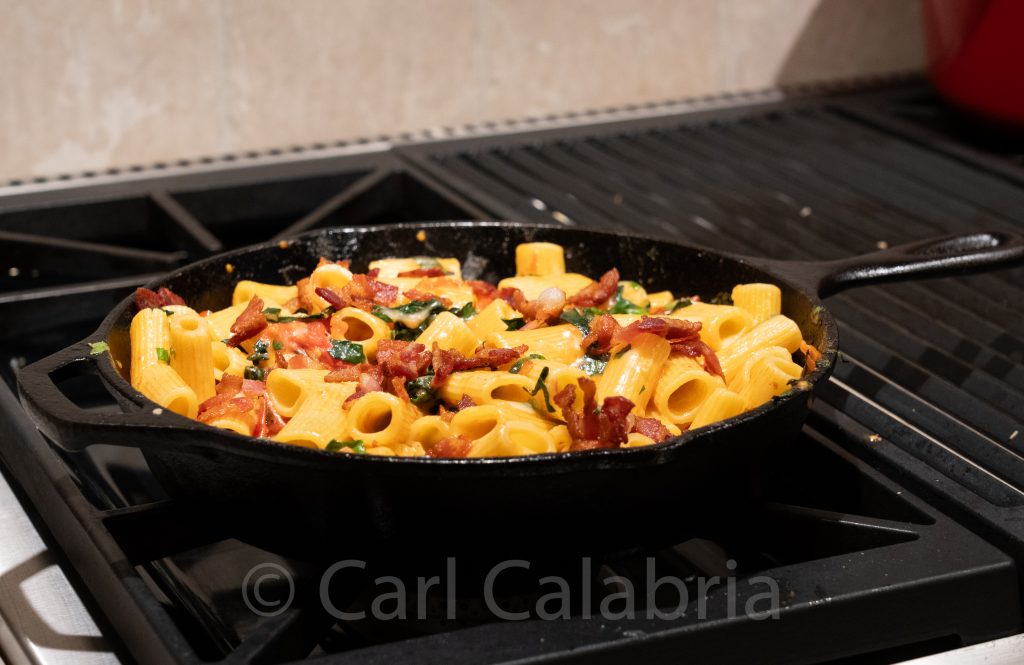
I am belatedly memorializing a delicious meal that Jeanine prepared earlier this week. Since she rarely makes the same dish twice in a year, I am saving this image to suggest that this is one worth repeating on a more frequent basis.
I am belatedly memorializing a delicious meal that Jeanine prepared earlier this week. Since she rarely makes the same dish twice in a year, I am saving this image to suggest that this is one worth repeating on a more frequent basis.
Today’s River House project was the installation of the island vent hood. The work was fairly straightforward with the most time spent ensuring that the vent was perfectly plumb and sealing the ductwork. I got a good upper body workout as it was necessary to hold a number of different components overhead while screwing them into place. Once installed, I had to open up the controller board and set a jumper to limit the maximum fan speed to 390 cfm. If you go over 400 cfm then you have to install a make-up air system which is something we do not need and didn’t want to be forced into. The hanging blue tape is to keep taller folks from running into the glass canopy before the island is installed. As it stands, I can just walk under it without banging my head.
Our double oven was delivered today. Of all the components going into our new home, it had the longest lead time of more than a year. As if to ensure it was here to stay, I immediately installed it, a task easier said than done given its weight of 333 pounds. Working alone forces you to always have an approach that does not rely on brute force. In this case, I built a temporary platform out of scrap lumber so that I could slide the oven directly into its opening. None of the cabinetry I have built has more demanding tolerances than the one for the double oven. It has to be dead plumb, dead level, and perfectly square in all orientations. If any one of these attributes is off by even the slightest amount, it will show up as a problem with the installation. I am happy to report that the time I spent making sure that the cabinet was just right resulted in a perfect fit. Also operational now is our microwave. We debated for some time if we should even have one in the kitchen. The new oven has a steam heating feature which is the healthiest way to reheat foods, the primary task which we have used the microwave for in the past. In the end, we decided a microwave would be convenient but need not be large and we wanted it to be located for convenient use. Our Road House has an under counter unit with automated drawer, a perfect solution for three foot tall people but a terrible location for anyone taller.
The bamboo plywood I am using is constructed of three plys. The front and back are 1/8″ thick vertically oriented laminations. The core is 1/2″ thick with laminations that run perpendicular. Whenever I need edge facing, I cut the top and bottom layers off leaving the core as waste. Having saved up all of these half-inch strips, I glued them together to create an end-grain cutting board. Jeanine liked it so much that she wanted me to make an entire bench top using this technique. It is a great idea but would represent a very time-consuming effort and perhaps one I could tackle well after we have moved in.
Precordial catch syndrome (PCS) is a non-serious condition in which there are sharp stabbing pains in the chest. These typically get worse with inhaling and occur within a small area. Spells of pain usually last less than a few minutes.
The underlying cause is unclear. Some believe the pain may be from the chest wall or irritation of an intercostal nerve. Treatment is usually via reassurance, as the pain generally resolves without any specific treatment. Precordial catch syndrome is relatively common in children between the ages of 6 and 12 and is less common in adults. While in my twenties and thirties, I experienced a half dozen or so episodes.
Yesterday, while working on a ladder in the basement of the River House, I had a PCS event. Given the spotty cell service there and the proximity to Emerson Hospital, I decided to drive to the emergency room out of an abundance of caution. It has been more than thirty years since I last had an attack and I thought it better to be safe than sorry. I arrived in under 5 minutes and was immediately connected to an EKG monitor which showed no signs of heart anomalies and my pain had all but subsided. Much ado about nothing but interestingly, no one at the hospital suggested PCS as the cause and were intent on following up with a bunch of tests and x-rays that would have been pointless. While I truly appreciate being evaluated so quickly, once it became apparent that I was not having a heart issue minutes turned into hours while waiting for my blood work to come back. I eventually decided to disconnect myself from all the monitoring equipment and check myself out.
Our new home uses a Zehnder ERV (Energy Recovering Ventilation) system to provide continuous fresh air to the very tightly sealed building. Today, I installed the exterior intake and exhaust vents which look and act like nostrils. I then powered up the system for the first time. Everything worked as expected and the system self-test confirmed that the unit can deliver its maximum specified 600 cfm of airflow. At this rate, all the air in the house could be replaced with fresh air once every hour. The recommended rate of exchange is once every three hours so we will operate the system at 200 cfm.
Mount Mansfield is the highest mountain in Vermont with a summit that peaks at 4,393 feet (1,339 m) above sea level. Maya originally planned to do a solo ascent last weekend but was joined by Nicolai who saw an opportunity to train for his attempt to summit 18,996 Cayambe Volcano in Ecuador this fall. He will be making the climb to raise money for the Range of Motion Project (ROMP) whose mission is to ensure access to high-quality prosthetic care for underserved people, improving mobility and independence. Nico used the climb to shoot a fund-raising video with Maya as his videographer. Should you wish to support this cause you can use the link below to do so.
As planned, our new septic and pump chamber tanks were delivered and installed today. Offloading and placement of the tanks took less than 30 minutes, a testament to the careful preparation work. Since septic systems are based on gravity flow, any discrepancies in elevation will result in compromised function and must be corrected at this stage. Happily, the tank heights were perfect and the remainder of the day was spent connecting the tanks and beginning the backfill work.
Excavation for a new septic tank and pump chamber took place today at the River House. The addition of our attached garage forced us to relocate the existing ones because they no longer met the setback requirements. The tanks are due to arrive on site tomorrow and we are hoping to have the septic system operational by the end of the week. That leaves water as the last service we need to connect to the house. We may choose to put this off for some time since it will involve tearing up the driveway and we still have many trades coming and going on a daily basis.
One of my favorite things about living in Concord is that we have our own electric utility, the Concord Municipal Light Plant (CMLP). Today, the line crew above connected our new underground lines to the grid and we now have power throughout the house. All the folks at the CMLP are extremely customer focused and it is such a pleasure to work with them. Trying to get anything done with Comcast, Verizon, National Grid, or any other major utility by contrast is an exercise in total frustration. These guys arrived exactly when promised and 30 minutes later we had power to the house. 15 minutes later they had removed the overhead wires that have been providing temporary power for almost two years.
The bamboo plywood I am using to build the cabinetry for the River House is available in a natural or carbonized version. We selected the darker carbonized color for our project and I was befuddled when the first shipment arrived with a few sheets of natural mixed in with the carbonized. I even found two sheets that were natural on one side and carbonized on the other. Earlier this week, I received a make-up shipment to replace the product that was damaged during the initial delivery. To my dismay, the color did not remotely match the material I have been building with. I sent the company a detailed e-mail expressing my frustration and asking them to explain what was going on. They insisted that the replacement sheets were carbonized even though they looked like the natural version to my eye. Fast forward one day and I happened to turn over a sheet of plywood I was about to cut. The mystery was solved the instant I saw the outline of the hard core foam insulation slab that I used as a sacrificial base when cutting sheets with my track saw. It was apparent that the plywood changes color dramatically when exposed to air, presumably as moisture is absorbed.
Hardscaping for the River House will make extensive use of natural stones. Jeanine and I visited a stone yard yesterday where we reviewed the inventory and learned all about how large boulders are cut into slabs. Slabs can be 7 inches thick for stairs or 2-3 inches thick for patios. We will be using both types. Pictured below is the saw used to make the cuts. It is conceptually similar to a bandsaw except it is oriented horizontally and uses what looks like a rope instead of a band. The rope has diamond-impregnated beads every few inches.
I have been working on the new house 7 days a week for several months now. Today, I took the afternoon off to go stone shopping with Jeanine. Our patio area will feature some massive stone steps, all to be cut from a single ginormous boulder. It was very fun checking out all the possibilities and learning how the stone is cut. Later we joined friends on an evening birdwatching walk through Great Meadows. We were hoping to see Night Hawks but they never showed up. Instead, we were treated to a very beautiful Green Heron.
The pantry in our new house will feature open shelving from floor to ceiling on one side. In total, there will be six shelves, each 8ft long. Jeanine likes the look of thick shelves so I am laminating two pieces of plywood together faced with a 1/8″ thick veneer. Pictured here is a glue-up of three shelves at once.
The front door to our new house is sheltered by a small portico. Today we installed a single 5-1/4 thick slab of bluestone as the floor for that area. Working with a stone that weighs over a ton was no easy feat but in the end, it fit perfectly into the opening which was lined in a copper pan and sloped downward to shed water. Jeanine was on hand to film the installation which took about an hour in total. Our past homes have all incorporated smaller stones set in mortar which are much easier to install and significantly less expensive. Over time, however, the constant freeze-thaw cycles experienced during the winter lead to the failure of the joints. The slab we installed today should last for hundreds of years.
Last week the Flexzilla air hose I use with my portable compressor developed an internal bulge for no apparent reason I could ascertain. The hose, manufactured by Legacy Manufacturing, carries a 5-year warranty and naturally, I purchased it nearly 6 years ago. The fact is that I have used the hose more in the last month than since I acquired it. I decided to file a warranty claim given how little use the hose has seen and was pleasantly surprised when I received a prompt reply stating that they were sending me a replacement. This is an example of a company doing the right thing for its customers. They can now count on my business for life and I can highly recommend Legacy products to others.
Jeanine assisted me today as we installed 36 smart light switches throughout the River House. Each switch is a programmable dimmer with an occupancy sensor that can be accessed over the Wi-Fi network for home automation functions. She prepped them while I installed them which made the job go twice as fast as it would have had I been doing the work alone. Towards the end, the skin on my fingers was starting to blister from tightening so many twist-on wire nuts (4 per switch) and she took over that job as well. Next, I taught her how to apply the hard wax oil we will be using on all the cabinetry and she finished one of the panels that will surround our freezer. We wrapped up the day by making a catalog containing the QR code for each light switch to facilitate future programming once we have Wi-Fi enabled. It is really the first time we have worked on the new house together and I really enjoyed working with her.
Jeanine returned today from a week-long visit with her sister Susan who lives in Burlington, Vermont. They had all kinds of fun including a visit to the Happy Bird Poultry Farm. I have been so busy working on the River House that time has passed quickly. Even so, I missed her and am glad she is back. I guess that would make me the happy bird.
Kyle shared this photo of his blender which was not up to the task of making his morning smoothie. Fortunately, the company has offered to replace it for free.
I completed the tall kitchen cabinet carcass for the double oven today. So far it has been the most time-consuming to build. All but one of the front faces required veneering, the “shelf” which supports the ovens had to be designed to support a 350-pound load, and the cavity had to be dead plumb, level, and square. It is also the heaviest single item I have built so far which made it difficult to move and install. There will be a drawer below the ovens and a cabinet with two doors above it. Still needed is a filler strip on the left to close the gap to the wall which is one of the few in the entire house that is not perfectly plumb; argh. Even though it fought me almost every step of the way, I am extremely happy with the finished product.
It is said that woodworkers basically take big pieces of wood, cut them into smaller pieces, and then glue them back together. Therefore, if you want to make fine things out of wood you need to master the art of gluing. Apply too little and your joint will fail. Apply too much and you will have a time-consuming gooey mess to clean up. After 40 years of practice, I am prepared to say that the glue lines pictured above are as close to perfection as you can get. You are actually looking at two plywood panels, each with a 1/8″ veneer glued to the edge. The veneers are placed back to back and the pair of panels are clamped together as cauls for each other. If you apply exactly the right amount of glue, distribute it evenly, and apply uniform clamping pressure you will be rewarded with the tiniest bead of squeeze-out confirming full coverage. The shims placed under the bar clamps keep them out of the glue preventing rusting of the clamps and staining of the wood.
I completed the base for the kitchen island today. When the countertop is added it will create a seating area on one side and have the induction cooktop placed on the other. Unlike the other cabinets in the kitchen, the island will sit on top of the finished floor. Therefore, I have not yet fastened the end caps or the back panel to the drawer carcass to keep the weight manageable; it would be very difficult to move fully assembled. The end cap on the kitchen-facing side includes open shelving for frequently used spices and cooking oils. Should we be so lucky to entertain toddlers at some point, I am sure this will be a favorite point of interest and I already have some child-proofing ideas in mind.
We deliberately pulled our electrical permit in the final week of 2022 so that we would not be subject to new 2023 code requirements that do not allow for kitchen island-mounted outlets. The new regulations only allow for outlets mounted on island countertops which is the last place I would pick to put an outlet, pop-up, or otherwise. The outlet within the seating area will include 2 USB-C charging ports and will not be visible from the dining and living areas. The other outlet will be for cooking-related appliances that are temporarily used on the island.
With these choices, we have a single island with two personalities. Viewed from the dining/living space, it presents clean lines and no clutter. while the kitchen end is all about the business of cooking.
If sawdust production is any measure of my cabinet making progress, I am 30 gallons in, closer to 50 if you include the contents of my dust collection system bin. Most of this was generated from my router table while machining lock miter joints. It is the only major piece of equipment I have that is not yet connected to my dust collector. I plan to rectify this before doing any further routing and hope to have the necessary parts within the week.
The kids joined us at the Road House for dinner to celebrate Kyle’s 31st birthday. Jeanine cooked up a feast including a peach-tomato-basil salad, fresh corn risotto, and beef tips. Maya was here for most of the day doing upkeep on her tiny house which she was proud to show off after dinner. I spent most of the day at the River House continuing with cabinetry work. Busy schedules have prevented us from gathering as a family for several weeks and it was nice to catch up with everyone. Kyle has been promised a promotion to manager within the year at his job and is now renting out his basement to a couple and their two puppies. He is planning to take a week-long vacation in Montana after attending a wedding there. Nico is in training for his upcoming climb of the 19,000 ft Cayambe Volcano in Ecuador and for the Amp Futbol Cup in Warsaw, Poland as a member of the US National Team. Maya will be climbing in Vermont next weekend and is planning a trip to Olympic National Park later this month. The shoulder injury she sustained mountain biking will require arthroscopic surgery and she is looking into the best options for having that procedure.
The kitchen island in the River House will be supported by four 5″x5″ columns. I am making them out of 3/4″ thick bamboo plywood using a lock miter joint at each corner. Pictured above is a cross-section of the joint taken from a thin slice I trimmed to square up the end. It looks rather complicated but can be made with a specialized router bit. Setup is a little tricky but once bit height and fence depth are properly adjusted things move along with little additional fuss. The only negative side to working with bamboo is that it dulls cutting tools very quickly. By the time I machined the 16 panels I needed, my once very sharp miter bit was groaning at the prospect of more bamboo. I must say, I am very pleased with the way the columns turned out and am now planning on using this joint for the construction of the stair treads and possibly for all drawer boxes as well.
The bamboo plywood I am using to construct all of the cabinets and built-ins for the new house has been a pleasure to work with save for the fact that it wears out carbide-tipped tools very quickly. Not so pleasant have been all of the mistakes made by the supplier. (1) Selected a carrier that did not have the right equipment to provide the contracted delivery method. (2) The second “rescue” carrier had the right equipment but arrived on site with the wrong kind of truck on their first delivery attempt. (3) When it was finally delivered (several weeks late), every single one of the 36 sheets had some form of water damage. (4) We ordered the carbonized color (darker one above) and received several that are of the natural color). We even received some sheets that are carbonized on one side and natural on the other, which is not even a product that the company sells. The photo above is of two sides of the same board! Thus far the company seems prepared to make things right so I am just rolling with the punches for now. I have been cutting off and scrapping water damaged sections or using them in non-visible locations. The mixed color challenge will be the most time consuming to address as it will required staining the natural boards to match the carbonized.
Twenty years ago, I enjoyed watching a television series called Boston Legal. The show was about the fictional law firm Crane, Poole & Schmidt whose Boston office was located at 500 Boylston St. Today, I had a meeting there with the founder of a venture capital firm and made the connection as I approached the building.
I found this little fellow lifeless on a window sill in the River House. All of the operable windows there are in their venting position to allow the house to dry out. The plaster, paint, concrete, and many other construction materials have a great deal of latent moisture that needs to be shed. We cannot begin laying the floor until the indoor humidity has stabilized at a reasonable level. The vented windows let in a lot of insects but they do not seem to be able to find their way out again. Fortunately, we should have our AC up and running in the next week or two which will allow us to close all the windows. As I am typing this, I just realized that we have screens for all the windows and there is no reason not to install them now.
The front door assembly was the final missing element of our new home’s exterior. It was installed today but not without challenges. Due to the way it must be tipped into position because of its extreme weight the opening height has to be larger than the published rough opening. Mathematically speaking, the space needs to be sized to equal the hypotenuse of a triangle with a base equal to the width of the door assembly and a height equal to the height of the door assembly. When the foreman of the five-man installation crew found me in my shop to inform me that the door would not fit, I simply grabbed one of my battery-operated saws and followed him upstairs. I have learned to roll with the punches through the course of our build. In less than 20 minutes, I was able to increase the size of the rough opening and the door assembly was placed into postion. Even though it is fully functional as-is, the crew will return on Friday to remove and reinstall the assembly so that it can be anchored more securely and raised up higher so that the door will have more clearance above the finished interior floor (to accommodate a rug).
When we sold our home on Mattison Drive, I left my old table saw with an attached router table for the new owner. I was not interested in trying to move that 20-year-old behemoth out of the basement. I replaced the table saw shortly after moving into the original River House, but the router table has been a low priority until I decided I would be fabricating our stair treads using a lock miter joint for which it is essential. Router tables are invariably a DIY construction project as I have yet to find a decent one fully configured. Mine uses a cast iron table top and mobility stand from Harvey. The router is a Bosch 2-1/4 horsepower unit and the router plate and lift are made by Jessum and sold under the Kreg brand. The Harvey fence I ordered will not arrive for another several weeks so I will be using my old Incra fence until them. My 40 year old Craftsman machinists tool chest proved the perfect solution for organizing and storing all my router bits and tools. Assembling and aligning all of the components took the better part of 4 hours after which I returned to cabinet making.